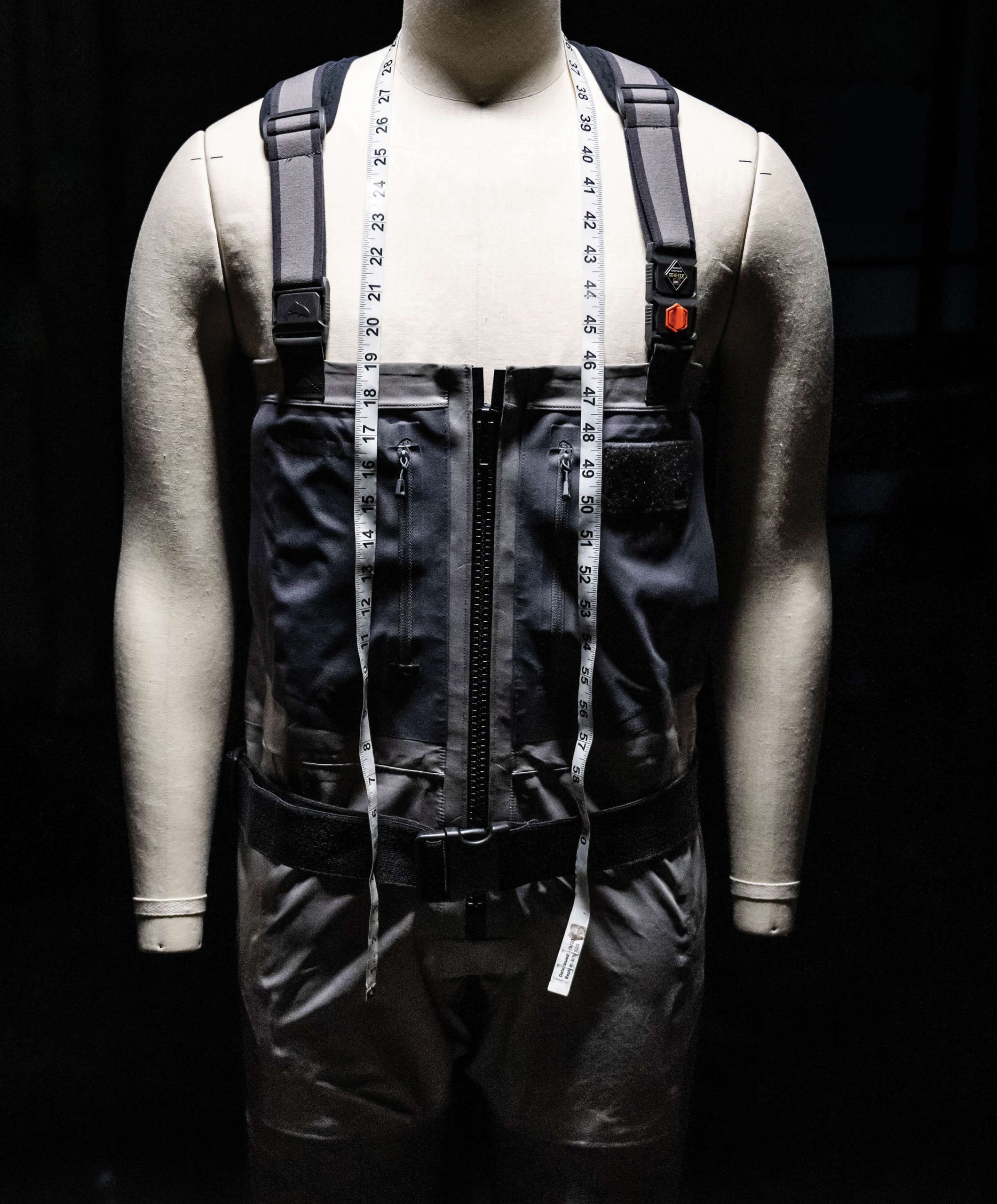
01 Feb The Wader Makers
inUpon walking through the front doors of the Simms headquarters in Bozeman, Montana, a passion for angling is immediately apparent: It permeates the very building. There’s the latest merchandise on display, an entire wall filled with best-in-the-business awards, and a brief history of the company as told through its pioneering fly-fishing products. But, behind all this, literally framed by floor-to-ceiling windows, lies the centerpiece of that passion — a state-of-the-art production facility where the iconic fishing firm makes high-end waders. They’re handcrafted here by a 45-person team of dedicated anglers known simply as “the wader makers.”
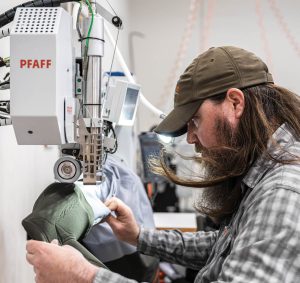
Former fishing guide Kyle Dresser works on a new pair of Gore-Tex waders in the attachment department at Simms. Photo by REX MESSING
Founded in the late 1970s in Jackson, Wyoming by fishing guide and entrepreneur John Simms, the company was born of the need for usable products for serious anglers. Simms started working with neoprene to keep gravel out of his fishing boots — which developed into neoprene hip boots and then into full-fledged neoprene chest waders, the first on the market when they debuted in 1980. A serial innovator who also created the Life-Link ski patrol shovel and Croakies sunglass holders, Simms was, once again, on to something. The waders were revolutionary: They kept anglers warm in chest-deep water and were credited with extending the fishing season earlier into the spring and later into the fall, putting more money into the pockets of fly shops and guides during these previously slower times of the year.
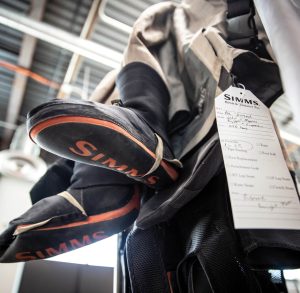
In addition to producing several lines of waders, Simms repairs gear at its production facility in Bozeman, Montana. Here, a pair of waders hangs after a repair. Photo by JOHN FRAZIER
On the cusp of his next innovation, Simms sold the company in 1993 to K.C. Walsh, who promptly relocated it to Bozeman, a location often considered the country’s epicenter of fly fishing. At the time, Simms was developing waders made with Gore-Tex, a relatively little-known waterproof and breathable fabric used mostly in winter clothing and rain gear. When the company’s first Gore-Tex wader hit the market in 1993, it was, again, revolutionary. While neoprene waders were warm and functional, they were tight to the skin, often making them too hot in warmer climates. They were also damp inside, making them hard to keep, well, fresh — the neoprene stink was real. The new Gore-Tex waders were lightweight, completely waterproof, and surprisingly breathable. It didn’t take more than a few years for neoprene waders to disappear completely, changing the sport forever. Field & Stream magazine ranked the Gore-Tex wader as the number one innovation in the history of fly fishing.
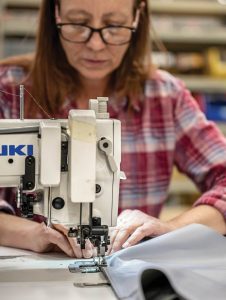
Julie Cleary is a seamstress at Simms, where she stitches handmade fishing waders together in a state-of-the-art manufacturing facility. Photo by REX MESSING
Simms quickly began to grow. Its high-quality gear developed a reputation for being well-built and long-lasting, made by anglers, for anglers. Today, the company operates a 70,000-square-foot flagship facility that was built on Bozeman’s west side in 2016. Employing more than 130 people, the company is a centerpiece of Montana-made manufacturing, producing everything from shoes to clothing to travel gear (not all of it in Bozeman), and Simms’ most well-known products — several different variations of its Gore-Tex waders — are still made in the Bozeman space. The wader production floors also include a full warranty department — where repairs are made — and a field-testing lab to try not only Simms products but also those of its competitors.
“Philosophically, it’s great to know that the waders being built in Bozeman are being built by individuals who are extremely familiar with the end use of what they are building,” says John Frazier, who runs public relations for Simms. “That’s genuine authenticity, and it’s part of what built Simms as we know it today.”
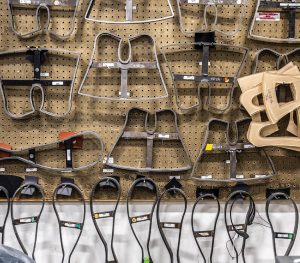
The Simms facility blends modern manufacturing with a nod to its long history in the fishing industry. Here, cutting dies hang on the wall in between use. Photo by REX MESSING
Julie Cleary has been a professional seamstress for 20 years and currently works at Simms, where she is a department supervisor on the wader-maker team. She’s been with the company for five years and comes to work every day knowing she is part of a small group of people who take pride in their jobs. “Simms gives me the opportunity to merge my talent and skill with my love of the outdoors,” she says. “The waders we make here in Bozeman really do give anglers their best days on the water, and I am proud to be a part of that process.”
It’s clear when watching the team at work that these are not factory workers. They are craftspeople with a specific skill set. Starting with a large square of Gore-Tex material, the waders go through a multi-step process during which the body panels are cut out, pressed, sewn together, taped, and reinforced with interior patches. Then, suspenders are sewn on, and the neoprene stocking feet are attached using a proprietary method that is an industry secret. Leftover Gore-Tex is repurposed to make items like wallets, leaving very little waste on the floor.
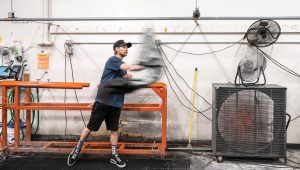
Production specialist Tyler Penman takes a pair of waders off of a drying machine at Simms. Photo by REX MESSING
Once the waders are fully assembled, they’re filled with water to test for leaks and then dried, boxed, tagged with an American flag, and shipped to more than 550 retailers and distributors worldwide. “The people that make waders here in Bozeman are the most essential piece of what makes a Simms wader stand above the rest,” says Kyle Dresser, a former fishing guide who works in the attachment department on the production floor. “Everyone who works here shows pride in what they make, and having it made by people right here in Montana is a special thing.”
The production floor is a vision of modern manufacturing. Each workstation has a tablet that tracks production during each shift, with incentives given for higher output. It’s a busy but comfortable space; workers look like they’re having fun. Simms worked with Bozeman’s Bridger Orthopedic to develop mandatory stretch break routines every two hours. The team also plays an important role in innovation. There have been many instances over the years in which team members have suggested changes or additions that make it into production — and they’re compensated for that as well.
“The team understands that the waders they build each day will play a role in the best memories and moments of anglers around the entire world,” says Frazier, noting that many of the wader makers are avid anglers themselves. “They are unbelievably skilled, they sweat every single minute detail, and they don’t settle for mediocrity.”
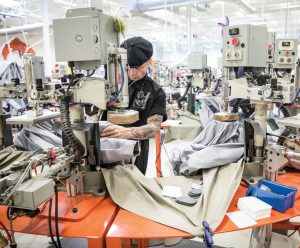
John Salcedo, a production specialist at Simms, helps finish a pair of Gore-Tex waders in the Bozeman facility. Photo by JOHN FRAZIER
Mediocrity isn’t really in the Simms vocabulary. The high-end waders — the top-of-the-line G3 Guide model that can run $900 — are known as some of the best in the business. There is a certain cache that comes with being made in Bozeman, where anglers flock from all over the world to fish the nearby blue-ribbon trout streams. “Simms are absolutely the highest quality waders you can buy,” says fly-fishing guide Joe Dilschneider, who runs Trout Stalkers in Ennis, Montana, near the banks of the famed Madison River. “They have gone through 40 years of evolution, and they are getting better and better.”
Dilschneider chalks the quality up to the extensive field-testing program the company operates. Ambassadors are often given products to test before they go to market, many logging more than 100 days on the river, allowing them to give invaluable product feedback. “At the core is Simms’ commitment to being the choice of professional guides and building the best gear for them,” he says.
For retailers, that can translate into sales. Anglers often want the gear that guides use, and it helps that some of that gear is made in Bozeman. “Simms might be the most iconic Montana company,” Dilschneider says. “There are customers out there who appreciate and love the fact that they are not only made in America, but are made in Bozeman. That is a factor for us, and for people visiting here.”
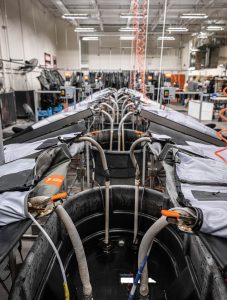
After the waders are assembled, they’re filled with water to test for leaks, then dried, and readied for shipment. Photo by REX MESSING
Griffin Litchfield works as a production specialist in the attachment department. He also spends his summers guiding in Alaska’s remote Togiak National Wildlife Refuge and has traveled to faraway places like Christmas Island to fish. He needs quality gear and is proud to help build the waders he personally uses. “Being able to manufacture gear for Simms and then getting the opportunity to make a living using that same product fills me with tremendous satisfaction,” Litchfield says. “Understanding how Simms waders are made and the attention to detail gives me confidence and pride in being a part of the wader-maker process.”
This is a familiar refrain from the wader makers, and their story is more than just another fish tale — it’s a way of life. Or at least the part of life that is warm, dry, and breathable.
Brian Hurlbut is the author of the Insiders’ Guide to Yellowstone and Grand Teton(Globe Pequot) and Montana: Skiing the Last Best Place (Great Wide Open), and his writing appears regularly in regional publications. He lives in Big Sky, Montana, where he enjoys the trails, mountains, rivers, and roads.
No Comments